Inter Granular Attack and End Grain Pitting Testing – The Importance of Test Piece Specimen Preparation.
Inter Granular Attack and End Grain Pitting Testing
The Importance of Test Piece Specimen Preparation.
IGA (Inter Granular Attack) and EGP (End Grain Pitting):
- In materials science, intergranular corrosion, also known as intergranular attack, is a form of corrosion where the boundaries of crystallites of the material are more susceptible to corrosion than their insides.
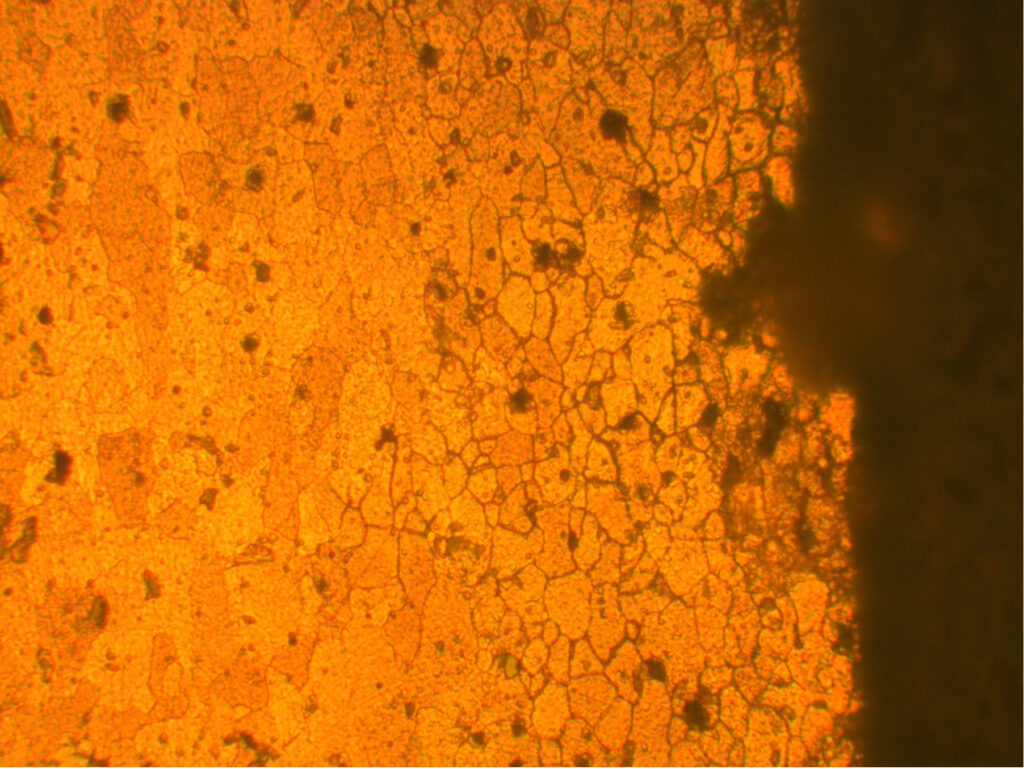
Fig 1. Intergranular attack and the formation of a corrosion pit at the surface of aluminium.
- Pitting corrosion, or pitting, is a form of extremely localised corrosion that leads to the random creation of small holes in metal extending from the metals surface. End Grain Pitting is specific to corrosion emanating from exposed end grain.
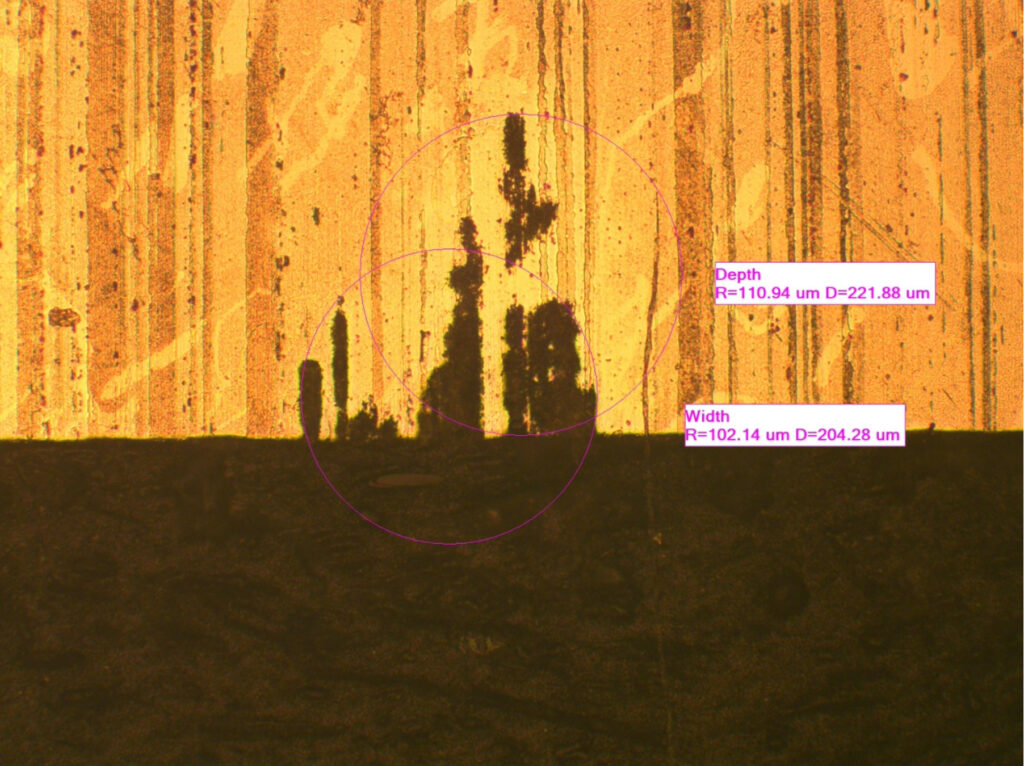
Fig 2. End grain pitting.
Background
Aluminium and its alloys are still very popular raw materials for the manufacturing of commercial aircraft, due to their high strength at relatively low density. However certain alloys are more susceptible to undesirable corrosion (IGA and EGP). Aluminium’s susceptibility to corrosion can be affected by heat treatment processes and induced by chemical processing. The combination of poorly corrosion resistant materials (post heat treatment) and potentially aggressive chemical processing result in inter granular attack and end grain pitting.
Heat treat:
Heat treating is a group of industrial, thermal and metalworking processes used to alter the physical, and sometimes chemical, properties of a material. During these processes, the properties of the material can become more susceptible to corrosion. Standardised testing investigates a materials resistance to corrosion. Susceptibility to IGA testing involves exposing the material to a known corrosive agent of which the material should be resistant. Metallurgical evaluations post exposure determines the materials performance.
Chem processing
Aluminium corrosion commonly occurs during chemical process operations involving surface finishing, mainly in preparation for paint application. The protective oxide film of aluminium is only stable in a pH range of 4.5 -8.5. However, many process solutions intentionally exceed this pH range for the purpose of cleaning, metal removal and subsequent smut removal. These process solutions are designed so as not to cause pitting or preferential etching. However, the susceptibility of aluminium to pitting depends on many factors, such as chloride concentration, pH control and initial surface condition.
Evaluation for corrosion caused during exposure to chemical process solutions is commonly performed on representative samples periodically. Where the end grain of material is most susceptible to corrosion and therefore evaluated for inter-granular corrosion and end grain pitting.
Importance of Test Piece Preparation
What has test piece preparation got to do with evaluation for IGA and EGP? Most commonly used specifications state the end grain surface is to be polished to 32Ra or finer (see below).
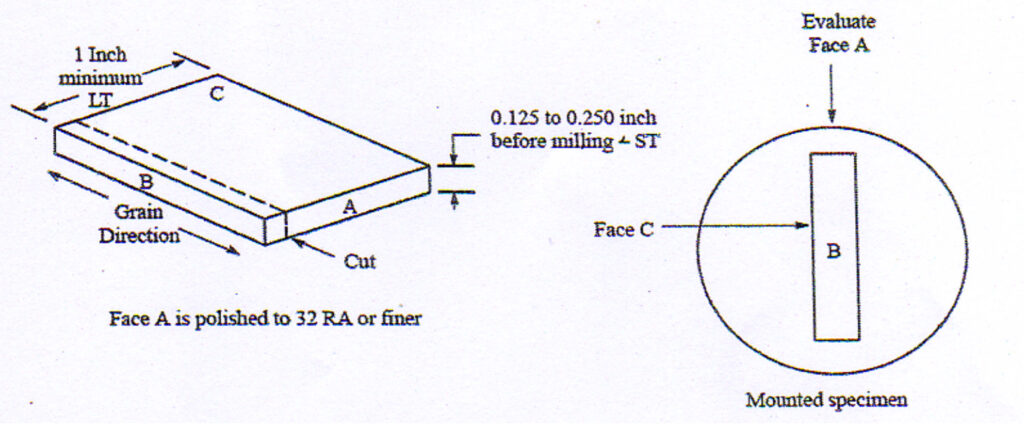
Fig 3. Orientation of end grain pitting and intergranular attack specimens.
Ra is measured using a profilometer. This is an instrument with a stylus that travels across the surface and measures the difference in height between the peaks and valleys of the surface profile. ISO standards use the term CLA (Centre Line Average), which is interpreted identically to Ra.
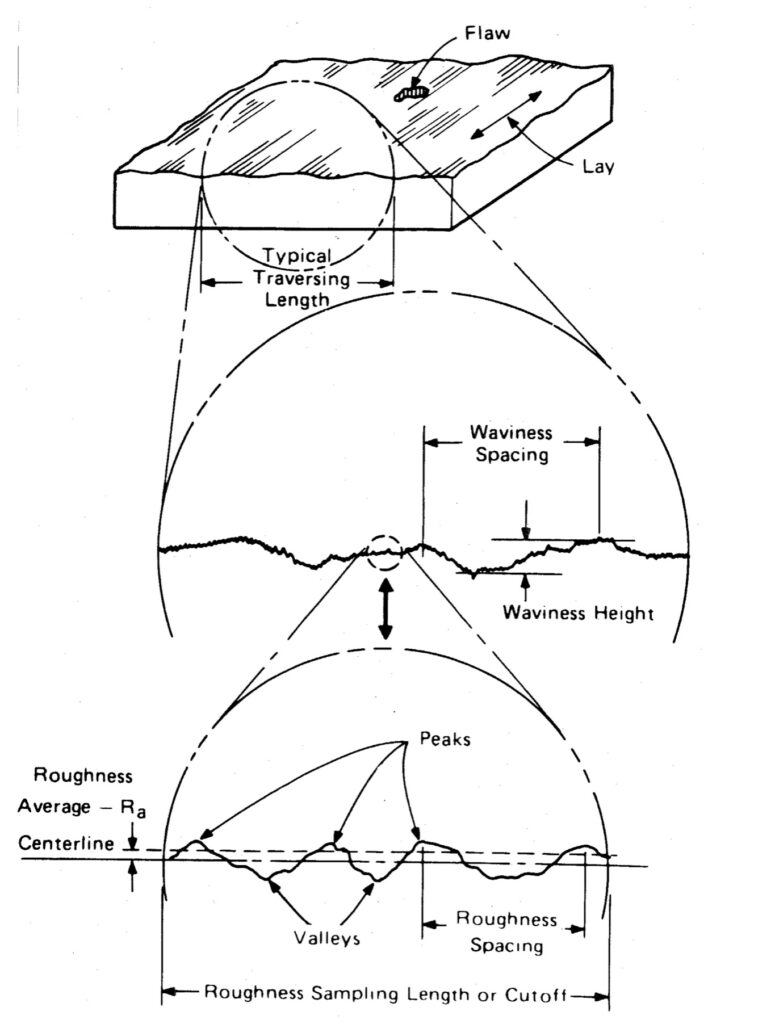
Fig 4. How surface roughness is measured along a materials profile.
A surface that is not finished to a high standard can have a rough surface profile from the cutting process. This rough surface profile causes difficulties with evaluation for pitting, in particular distinguishing between profiles due to corrosion and profiles caused when cut.
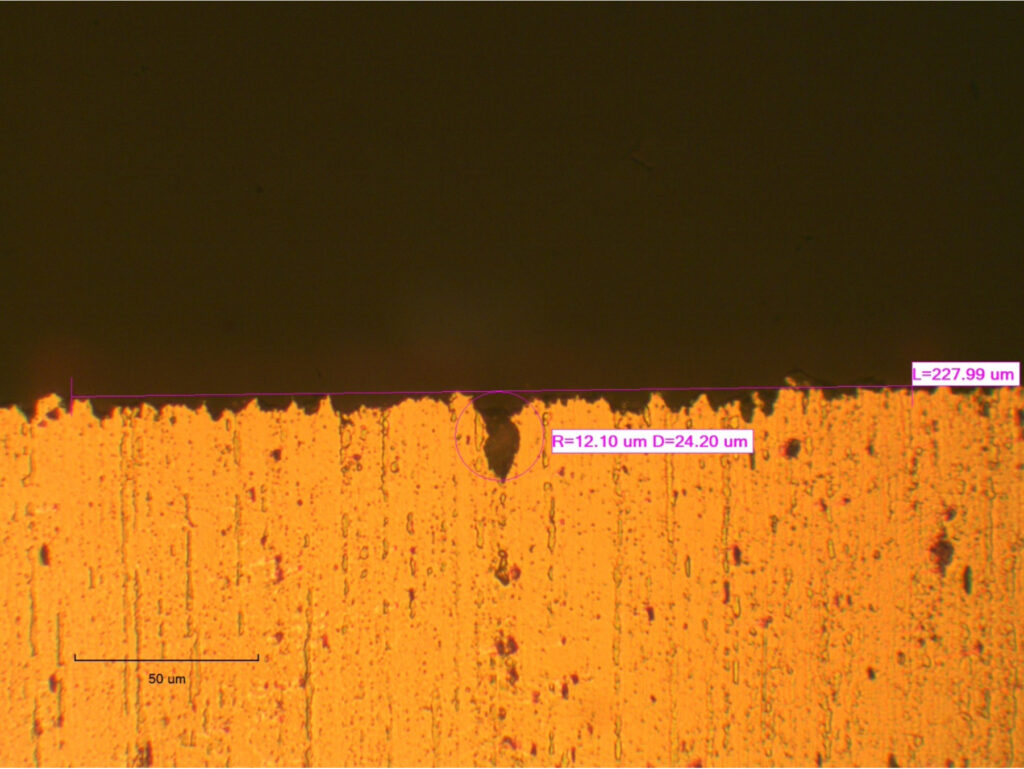
Fig 5. Rough profile at the end grain. This test piece was not polished.
Guillotined test pieces need the ends ground off prior to polishing as pressure from the guillotine can cause surface microcracks and edge rounding of the grain structure.
It is also important to ensure the integrity of the surface once polished. Scratches in the surface profile can make evaluation for end grain pitting more difficult (see fig 6).
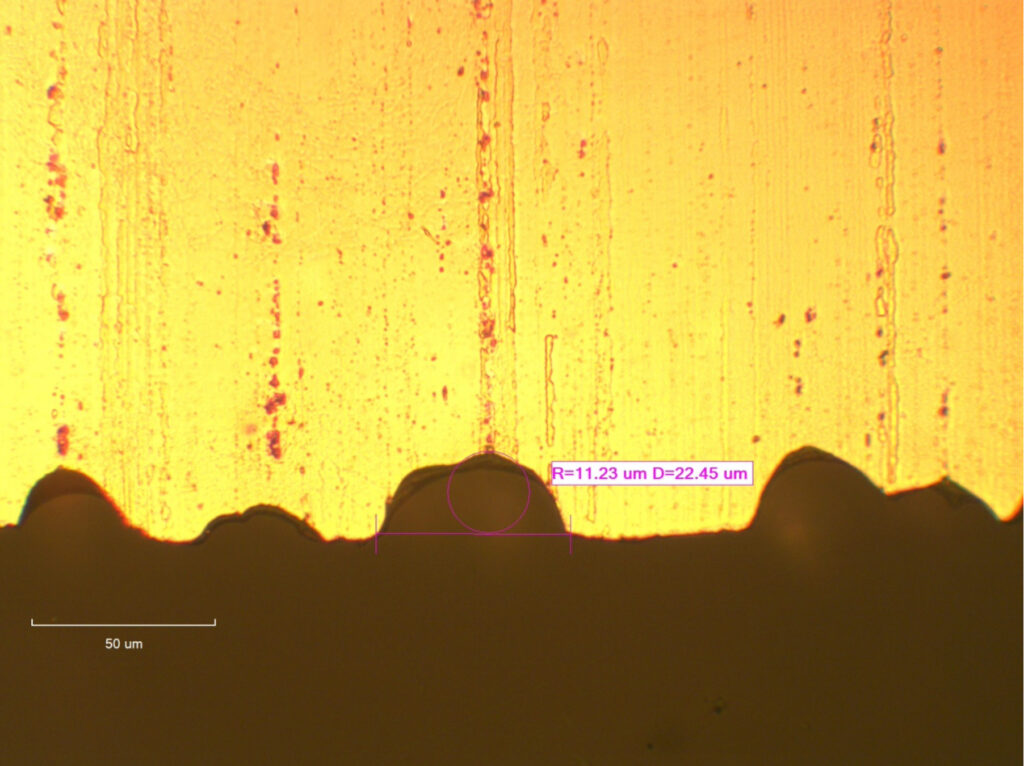
Fig 6. Uniform scratches in the end grain surface.
Conclusion
To conclude, it is necessary to prepare a surface with a flat profile (see fig 7), to ease evaluation of IGA and EGP. A rough or damaged profile could have defects which could be mistaken for pitting, resulting in a false positive result.
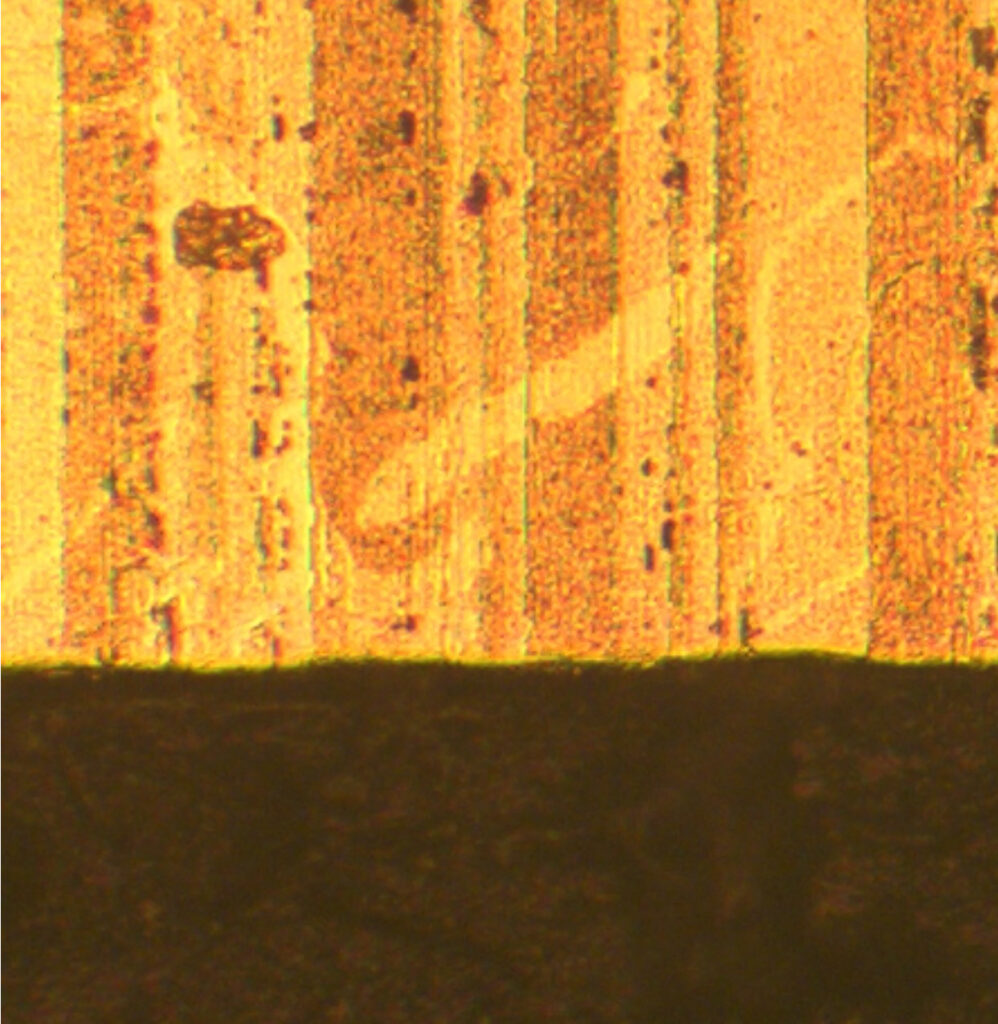
Fig 7. End grain with a flat profile.